The following is an article from Dirk Venter which appeared in the Ground Support 2023 Supplement
Ground support design cycle: an approach to increase safety and efficiency
By Dirk Venter, Epiroc
Introduction
Ground support is essential in an underground mine to ensure the safety of the workers and the mine. As the volume and depth of mining increase, the behaviour of the rock mass changes. Hence, there is a frequent need to adapt and re-design the systems and techniques used to support and control the rock mass.
This article provides an overview of the Epiroc approach to the ground support design cycle – an iterative cycle to design, implement and monitor tailor-made ground support systems to increase safety and efficiency in challenging ground conditions, allowing mining operations more time to mine.
Rock mass behaviour
As mines go deeper and mining volumes increase, the risk of damage to underground excavations increases. To protect excavations, ground support design and application are becoming increasingly critical to ensure the safety and productivity of mining operations. The behaviour of the rock is determined by the ratio of the field stress to the in situ rock mass strength. If the field stress in the rock wall is high relative to the in situ strength of the rock mass, significant deformation of the rock mass can be expected due to squeezing or rockbursting. Each of these distinct rock mass behaviours requires different considerations when designing ground support.
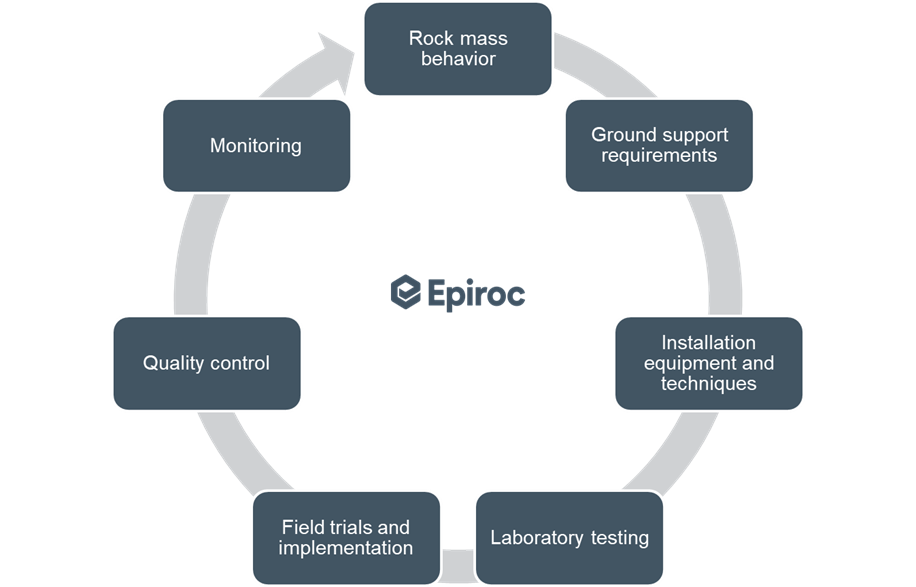
Ground support requirements
The primary objective of ground support is to mobilise and conserve the inherent strength of the rock mass so that it becomes self-supporting. Various elements are used to create a support system, including rock reinforcement and surface support. Rock reinforcement refers to techniques such as rockbolts and cables. Surface support refers to techniques such as shotcrete, steel wire mesh and steel straps.
In recent years, a significant development in ground support has been the design and implementation of yielding ground support. Yielding ground support systems are designed to control, rather than prevent, the movement of the rock mass during dynamic and longer-term displacement events as the energy and forces involved cannot be entirely prevented. Critical to the success of the ground support performance is the interaction between the shotcrete, welded mesh and yielding rockbolts which function as a complete system to hold, retain and confine the broken rock mass.Understanding the expected behaviour of a particular rock mass allows for the specification of the ground support system performance, according to three main parameters: load capacity, displacement capacity and energy absorption capacity. Other considerations for the selection of the best-suited ground support system includes rockbolt configuration and length, expected life of excavations, installation equipment, installation techniques and efficiency, installation quality and consistency, and operator training and skill.
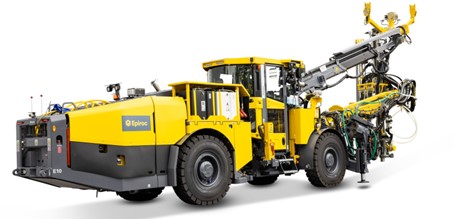
Ground support installation techniques and equipment
The performance of ground support systems depends on the installation quality. Therefore, the techniques and equipment used to install ground support need careful consideration. Modern bolting rigs, such as the Epiroc Boltec, offer the ability to install various types of rock reinforcement and steel wire mesh, allowing flexibility to select the best-suited support system as ground conditions change.
The installation efficiency of ground support has a direct impact on mining cycle productivity. According to a study conducted in 2016 (Haugen 2016), the ground support operations can comprise up to 57% of the mining cycle time. To fully optimise the ground support cycle, an all-inclusive approach is required that considers the installation equipment and techniques, rock reinforcement and surface support.
Laboratory testing
As the rock behaviour changes, the ground support loading conditions change. Different ground support systems perform differently under varying loading conditions. To get a better understanding of a particular system’s performance, laboratory tests are conducted using specialised test rigs. Laboratory testing provides a platform to perform tests with relative ease and frequency. The repeatability of testing and instrumentation quality that can be achieved makes them an invaluable part of the ground support design process, contributing to quality assurance and quality control, comparative test studies, determining system performance parameters, and research and development. It is important to note that laboratory testing cannot fully simulate underground loading conditions and other factors influencing the ground support system behaviour. This, however, is not the purpose of laboratory tests. The Epiroc test facilities in Johannesburg, South Africa, allow for the in-depth investigation of rockbolt behaviour under various loading conditions including dynamic, tensile, shear, and combined tensile and shear.
Field trials and implementation
Field trials are an irreplaceable step in the implementation of any new ground support system. Field trials aim to verify the performance of the system in an area representative of the expected rock mass and loading conditions. Trials may include pull testing of individual rockbolts and monitoring the ground support response to changes over time. Trials also provide a unique opportunity to optimise the quality and efficiency of the installation based on operator experience and feedback. Implementing any new ground support system can be associated with many risks and, therefore, needs to be well managed. Training is essential, ensuring that all aspects related to the correct functioning and installation of the system are well understood.
Quality control
The importance of quality control and quality assurance processes cannot be overstated. Quality assurance starts at the factory. The raw material is received and tested according to specification before it is released. Destructive and non-destructive tests are routinely conducted on samples pulled directly off the production line during the manufacturing process. Quality control certificates are issued and saved for record keeping and statistical analyses. Each rockbolt produced has full traceability back to the raw material batch from which it was manufactured. Audits are routinely conducted to ensure compliance with international manufacturing and management standards. Quality control is not just limited to the manufacturing facility. Regular quality checks during and after ground support installation are essential. Epiroc offers rockbolt systems with built-in indicators that provide visual confirmation of correct installation.
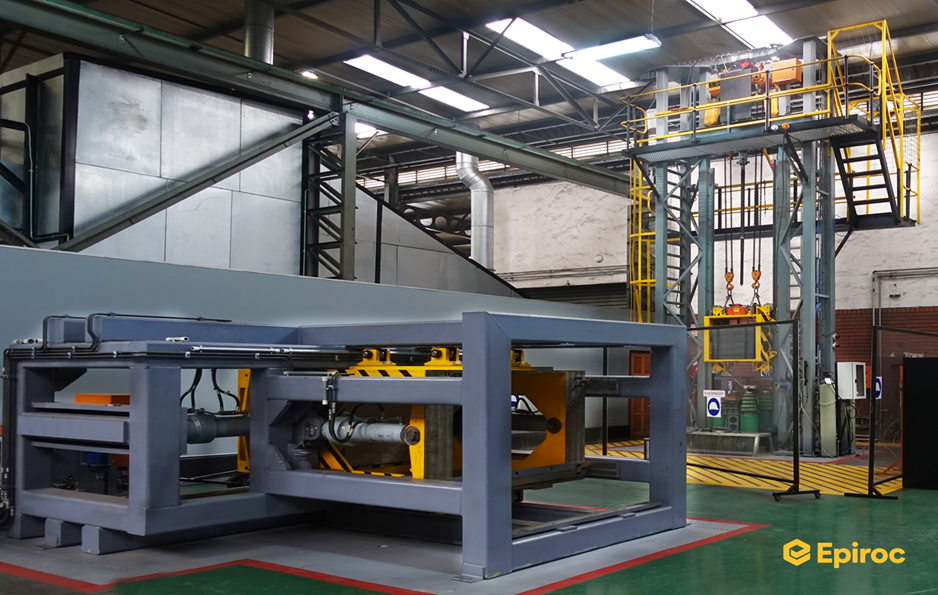
Monitoring
Monitoring is an essential step in the ground support design cycle. Following the excitement of a successful implementation of a new system, this step is easily overlooked. However, monitoring provides an opportunity to identify any changes in the behaviour of the rock mass and the ground support response. The development of digital solutions and communication technologies for application in mining is opening up exciting opportunities for implementing large-scale real-time monitoring. Digital rockbolt deformation monitoring systems aim to provide a better understanding of the ground support response and allow early intervention should ground conditions change. The learnings gained from analysing monitoring data provide valuable input for optimising and redesigning ground support systems based on the rock mass behaviour.
Conclusion
This article provided a brief overview of the Epiroc approach to the ground support design cycle. The iterative process aims to increase the safety and efficiency of mining operations, providing innovative ground support solutions for the most challenging ground conditions, allowing mining operations more time to mine.
Reference
Haugen, S 2016, ‘Rock support in a cut & fill mine – from the operational perspective of a mine manager’, in E Nordlund (ed.), Proceedings of Ground Support 2016, Luleå University of Technology, Luleå.
DL Venter, Epiroc, Australia